Foundry is nothing more than a process, known since 5000 BC of manufacturing metal parts by filling molds with liquid metals, these molds have cavities with dimensions similar to the part you want to produce.
There are classifications that define the foundry industry, these are: the alloy composition of the foundry and the casting process used. The alloy composition of the foundry is divided into ferrous and non-ferrous; the ferrous ones consist of alloys of iron and carbon which are divided into steel and cast irons, and the non-ferrous ones are those made of aluminum, zinc, copper, and magnesium. For the casting processes it is necessary to define the degree of precision of the cavities, the finishing, and the mechanical properties of the part.
The processes are chosen according to the mold that can be divided into metallic and non-metallic. For metallic molds the gravity and pressure processes are used. For non-metallic molds are used the methods of green sand, cold cure, Shell, and waxes, being the molds made with sand the most traditional. traditional.
In the green sand casting, there is in most cases the making of two halves, which, when joined, have the shape of the piece, before receiving the liquid metal the mold is coated with paint. In the Shell process, the mold is made of metal and is fixed on plates, these plates are coated with special sand and resin. In lost wax the molds are made of special refractory slurry, made with silica or zirconia mixed with binder and other components. Gravity metal molds are usually made of iron or steel and are used for about 100,000 times.
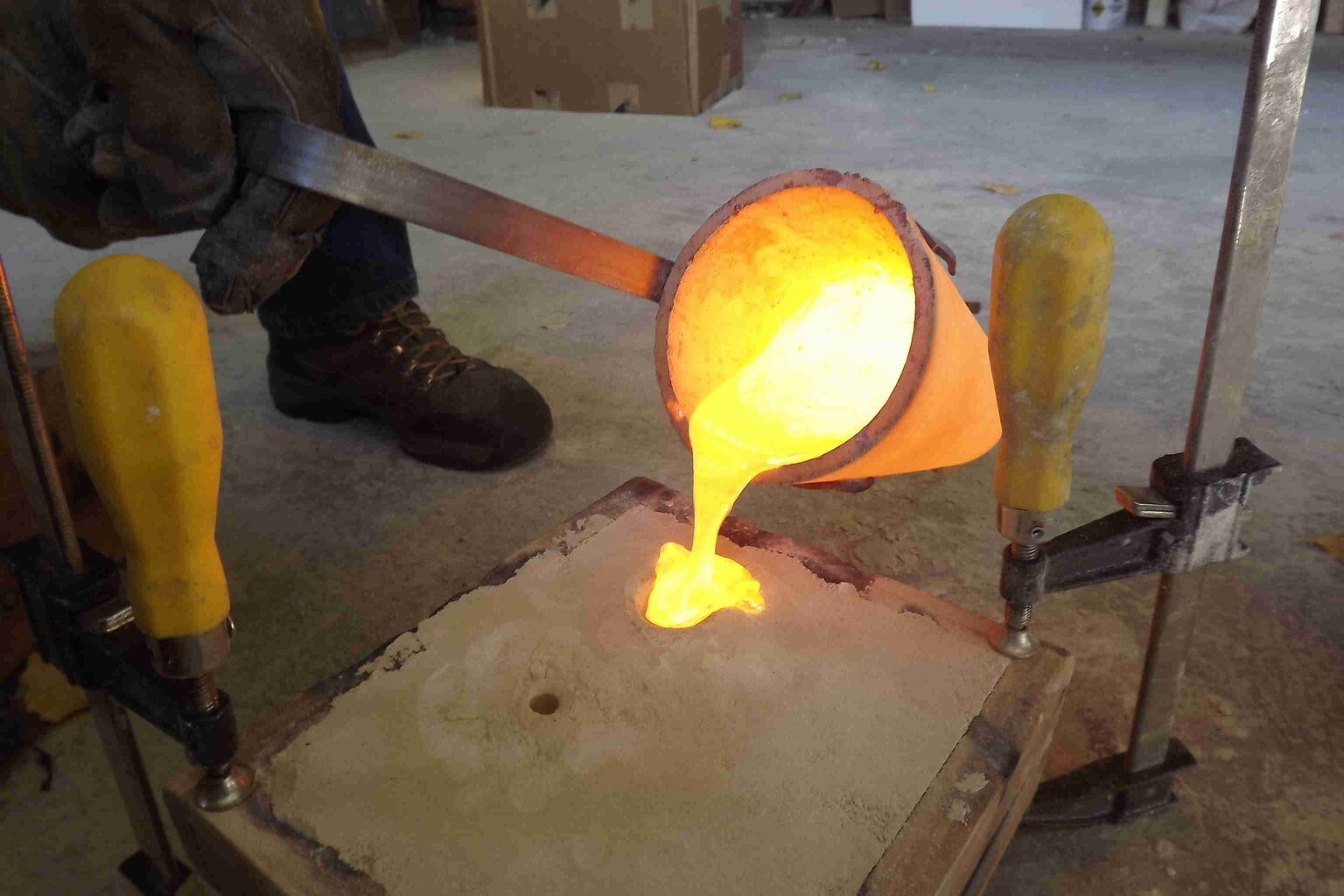
Foundry Paints
Foundry paints generally have resins in their composition that can act as binders and fixatives. The base of a foundry paint consists of solid materials in suspension in some dispersion medium (vehicle), liquid and depending on its characteristics, are applied by brushing, spraying, immersion, washing or spraying.
For the production of alcohol-based paints, we indicate the products Carbofen Resin and Respin Shellac, both of which present excellent performance in formulations and can participate in paints based on zirconite, graphite, lamellar aluminum silicate, alumina, magnesite, and iron oxide. For application in molds by means of washing, Carbofen Resin is ideal, as it has greater fluidity. For spray applications, where the paint cannot run off, Respin Shellac is more indicated, as it has less fluidity.
Our products are resistant to high temperatures, which is why they are indicated for iron and steel foundries, where permanent metallic molds would not resist excessive heat. The paints produced with our resins are intended to act on the surface of the mold or core, bringing some advantages such as:
- improves hardness and resistance to friability
- improves the aspect of the casting as to roughness, adherences, and cleanliness
- Reduce and/or eliminate the occurrence of surface defects such as veining, penetration, gas bubbles, erosion, among others
If you need more information about our products for foundry coatings, contact us now!