What do you think of when you hear the word “asphalt”? For most people, it is a brand-new road. However, “bitumen emulsions” or its interchangeable countertype, “asphalt emulsions,” has many other meanings than just road paving. In this post introducing bitumen emulsions, the following questions and statements will be covered:
- What is Bitumen?
- The Definition of Bitumen Emulsion
- What is an Emulsifying Agent and What Purpose does an Emulsifier have in an Asphalt Emulsion?
- Example of Products that are Anionic Bitumen Emulsifiers
- What are the Main Components of a Bitumen Emulsion?
- What is the Manufacturing Process of Asphalt Emulsions?
- How are Bitumen Emulsions Classified?
- Who is Responsible for the Classification of Bitumen Emulsions?
- How are Anionic Bitumen Emulsions Classified?
- The Charges of Asphalt Emulsions
- What is the Difference between Cationic and Anionic Emulsions?
- The Setting Times of Bitumen Emulsions
Each section is mostly self-contained. So, feel free to read the whole article or skip to the sections that interest you most. Happy learning!
What is Bitumen?
First, some terminology. The term bitumen is commonly known as “asphalt cement” or “asphalt” in North America. While in other parts of the world, the road paving mixture of sand, stones of various sizes, filler and bitumen is known as “asphalt.” For the purposes of this post, the terms will be used interchangeably.
At ambient temperatures, bitumen is a stable, semi-solid substance and in order to make a beautiful highway like the one displayed above, it has to be applied in an aqueous state. To make asphalt malleable and versatile, bitumen can be heated, dissolved in fuel oils or emulsified in water. However, for different reasons not all of these options are viable. Heating asphalt is expensive and dissolving it in kerosene, gasoline or the like results in pollution from volatile organic compounds (VOCs) and possible occupational hazards. So, the most cost-effective, environmental-friendly and worker-safe option is emulsifying the asphalt in water. By dissolving asphalt in water, a bitumen emulsion is created.
The Definition of Bitumen Emulsion
An asphalt emulsion is mainly a stable mixture of asphalt cement, water and an emulsifying agent. Thus, this mixture has bitumen droplets suspended in water with the aid of an emulsifier. The aqueous solution can be pumped into tanks for storage, mixed with aggregates to be applied to pavement, and can be used in several different ways.
The “breaking” is the unifying factor of all asphalt emulsions. This industry jargon describes the process in which water separates from bitumen after the asphalt emulsion is applied or mixed. For example, emulsions break:
- upon contact with aggregates (sand, filler, stones, etc.…) when mixing, or
- when sprayed onto a surface.
Also, bitumen emulsions can break in 3 different ways:
- by chemical destabilization of the emulsifying agent,
- simple evaporation of water, or
- a combination of both above-mentioned options.
It all depends on how the emulsion will be used and what is the desired breaking speed. Consequently, after the asphalt emulsion breaks and cures, the bitumen residue has the same durability, adhesion, and water-resistance properties of the original base asphalt.
If imagining a bitumen emulsion is hard, think of paint and shampoo. These are common examples of emulsions we use every day.
What is an Emulsifying Agent and What Purpose does an Emulsifier have in an Asphalt Emulsion?
The emulsifier is a chemical surface-active agent and formed of large molecules. Another interchangeable term for emulsifier is surfactant. These soap molecules are like tadpoles. They have an electrically charged head soluble in water and a hydrocarbon tail soluble in the liquid bitumen. Consequently, the ionic charge of the emulsifying agent surrounds the asphalt droplets. The result is a bitumen particle repelling others and remaining suspended in the water solution.
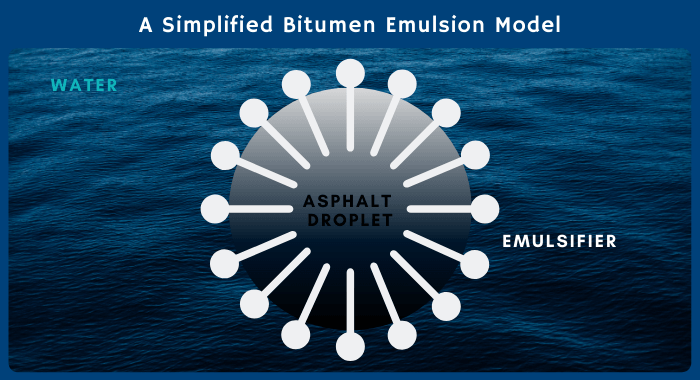
Furthermore, emulsifiers are also known as chemical surface-active agents. These surfactants are classified by their electrochemical charge. There are 3 types of charges: anionic, cationic and non-ionic. In the case of anionic emulsifying agents, the electrochemical charge is negative, while for cationic emulsifiers, the charge is positive. In the case of non-ionic, there is no charge. All three types are surfactants and in their own way, give stability to the bitumen emulsion by not allowing the asphalt to separate from the water in the solution.
For instance, by mixing an anionic bitumen emulsifying agent with water and asphalt, the anionic surfactant will give a negative charge to all the bitumen particles. Since opposite charges attract and same charges repel, all of the negatively charged droplets repel each other and remain suspended as distinct asphalt droplets in the solution. The same is true for cationic emulsifiers. The only difference is that cationic emulsions have imparted positive charges to all asphalt particles. An anionic emulsifier is highlight below as an example.
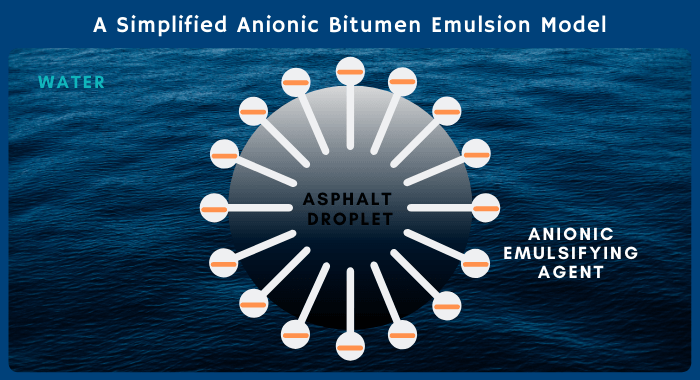
Examples of Products that are Anionic Bitumen Emulsifiers
Within Polytrade’s portfolio there are two powerful anionic bitumen emulsifying agents, such as Carbofen Gold, and Emulsifen G5000. As anionic surfactants, these products keep the asphalt droplets of microscopic size suspended in water. As a result, high quality and stable anionic emulsions can be manufactured with these eco-friendly products. The SS bitumen emulsions made with Carbofen Gold and Emulsifen G5000 are used in the production of:
- waterproofing and roofing products for several commercial and residential sites, as well as
- road surface binders, such as slurry seals, tack coats and many more.
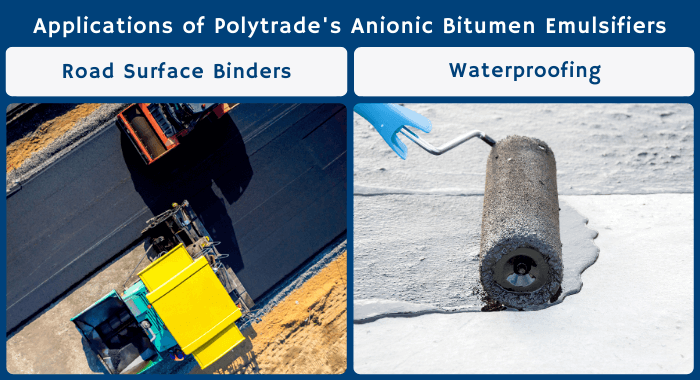
What are the Main Components of a Bitumen Emulsion?
Since a bitumen emulsion is essentially asphalt particles suspended in water, there are 3 main components to this kind of emulsion:
- Asphalt cement,
- Water,
- Emulsifying agent.
1) Asphalt Cement
The first and main element of bitumen emulsions is asphalt cement. Usually, 50 to 75% of the total emulsion consists of asphalt cement. Thus, it is not a surprise that some of its particular characteristics significantly affect the finished bitumen emulsion, which also have an impact on the efficiency of the base asphalt after application. For instance, the type of asphalt cement has an effect on the initial waterproofing ability of the pavement when applied to a road. However, there is no exact correlation between the potential to emulsify the asphalt cement and its properties, so trial and laboratory testing is essential to find the ideal mix for the desired application.
2) Water
The second component of bitumen emulsions is water. However, it is not normal drinking water. Conventional water used for consumption may not be suitable for asphalt emulsions, because minerals or other materials in the water can react with the properties of the asphalt cement and the emulsifier, resulting in an adverse reaction to the stability of the bitumen emulsion. Consequently, the expert recommendation to produce asphalt emulsions is using distilled water with a neutral pH.
3) Emulsifying Agent
The third component of a bitumen emulsion is the emulsifying agent. The product (or products) used as emulsifiers significantly impacts the properties of an asphalt emulsion. Not only does an emulsifying agent keep bitumen droplets suspended in water and determines its breaking time, the chemical compatibility of the asphalt cement with the emulsifier is also vital for creating a stable emulsion. Consequently, the chemical type and quantity of the surfactant used in the manufacturing process of the bitumen emulsion determine whether it is cationic, anionic or non-ionic and what applications the emulsion can be used for.
Finally, asphalt emulsion formulations can have other components added to enhance its properties. Some of these property-modifying materials are:
- polymers,
- latex, and
- acids.
But in a nutshell, asphalt cement, water and at least one surfactant are the basic ingredients that compose a bitumen emulsion.
What is the Manufacturing Process of Asphalt Emulsions?
As seen in the section above, asphalt emulsions are composed of three main ingredients. At the same time, several components can be added to enhance the properties of the final application. These materials are all taken into account when making a specific type of bitumen emulsion. Below is a straightforward illustration summarizing the manufacturing process of asphalt emulsions. The model is generic and does not take into consideration the type and classification of all available emulsions.
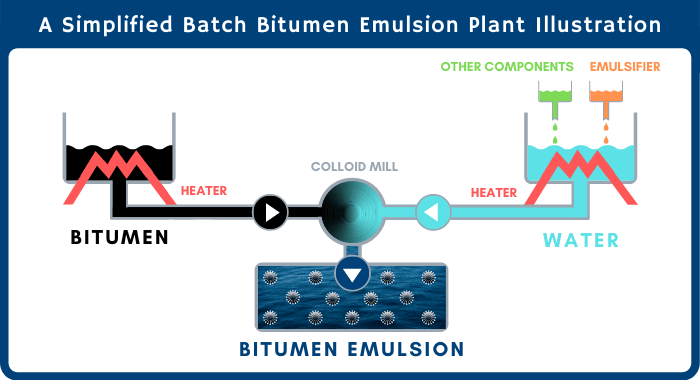
In order to suspend the asphalt cement in water, it has to be sheared into microscopic droplets ranging from 1 to 10 microns. This can be accomplished with the aid of a colloid mill or a rotor & stator. The process of shearing (or “cutting” bitumen) into microscopic particles happens in specialized plants that usually have a colloid mill to create these droplets that are smaller than the average 70 to 100 microns of thickness of a human hair.
Consequently, a bitumen emulsion is prepared by separately metering the heated asphalt cement, water, surfactant and other components into a colloid mill at preset temperatures and rates. The size of the asphalt particles and the quantity of surfactant affects the physical and chemical properties of the finished emulsion. Thus, the most monitored aspects of the process are:
- the temperature of the bitumen,
- rates of component addition, and
- timing of the blend.
How are Bitumen Emulsions Classified?
Asphalt emulsions are mainly identified by their charge and setting time. The most common charges are anionic, cationic or nonionic. And the usual setting times for emulsions are rapid, medium, slow or quick. But do not worry! These characteristics will be described in more detail in the next sections. The main idea here is to understand the most common set of prefixes and suffixes used to organize and categorize emulsions.
Other than charge and breaking time, bitumen emulsions are classified by asphalt penetration ranges, modification with special additives, their viscosity and storage temperatures. Below are two tables displaying some of the most common prefixes and suffixes in the industry.
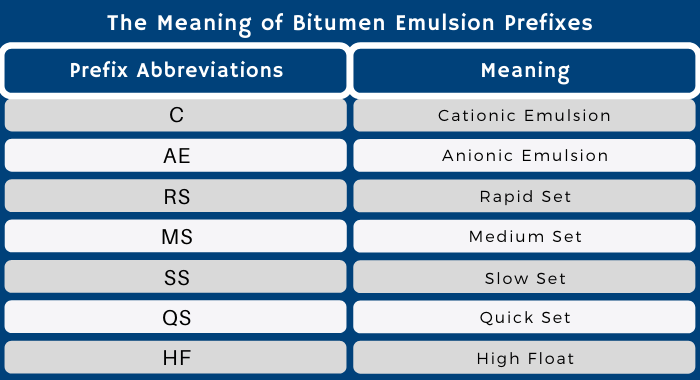
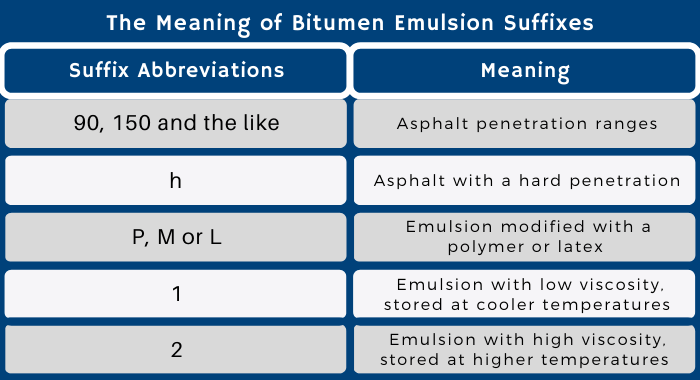
Example of a Bitumen Emulsion Classification
What are SS-1 and SS-1H bitumen emulsions? The guidelines supplied above explain it all.
For example, the “SS” in SS-1 stands for slow set, which is the classification of breaking time of the emulsion. Next is the “1,” which represents the characteristic this particular emulsion has of low viscosity. Also, the information that SS-1 emulsions should be stored at cooler temperatures is reveled.
Lastly, the biggest difference between SS-1 and SS-1H emulsions is the “H.” According to our table above, this letter describes emulsions that have a hard penetration grade. Or in other words, these are bitumen that are harder to emulsify due to their natural “hardness.” The lower the number, the harder the pen grade, while higher values indicate softer bitumen.
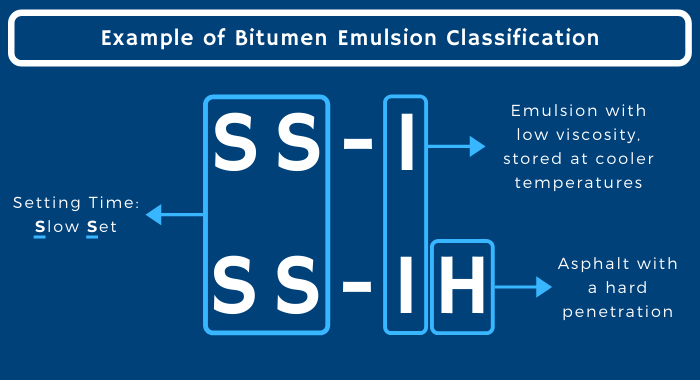
Who is Responsible for the Classification of Bitumen Emulsions?
In the US, two main institutions have standardized and defined how asphalt emulsions are classified, the American Association of State Highway and Transportation Officials (AASHTO) and the American Society for Testing and Materials (ASTM). The vast majority of highway agencies have adopted the harmonized system ASTM and AASHTO have established. However, like every rule has an exception, there are some proprietary and/or local designations.
Worldwide, innumerous institutions are dedicated to standardizing how asphalt emulsions, pavements and derivatives are classified, identified, and tested. These foreign institutions look up to AASHTO and ASTM and adapt their findings to the local context. For example, in Brazil, the Brazilian Association of Technical Standards (free translation), or ABNT for short, is the organization that is responsible for standardizing testing and classifications for all types of materials. Like emulsions, they adapt quality standards set by the American institutions to the reality of Brazil.
How are Anionic Bitumen Emulsions Classified?
As discussed before, asphalt emulsions are classified by their charge, setting time, modification, viscosity and storage. Below is a table summarizing the most common types of anionic bitumen emulsions.
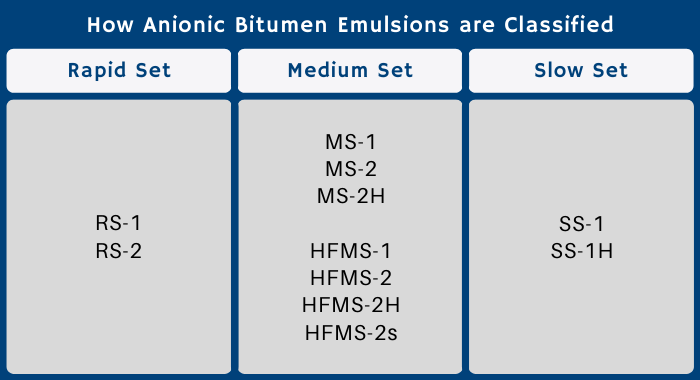
The Charges of Asphalt Emulsions
There are three possible charges for a bitumen emulsion:
- positive,
- negative, or
- neutral.
Thus, positively charged asphalt emulsions are identified as Cationic Emulsions. The negatively charged emulsions are classified as Anionic Emulsions. The third and less common group of asphalt emulsions is Nonionic, which have a neutral charge.
The importance of knowing the charge of a bitumen emulsion lies on its affinity to particular aggregates. Also, having knowledge of the charge is imperative in order to not mix positive and negative charges together. Since opposites attract, the emulsion would be useless if it sticks to itself instead of adhering to the aggregates during application.
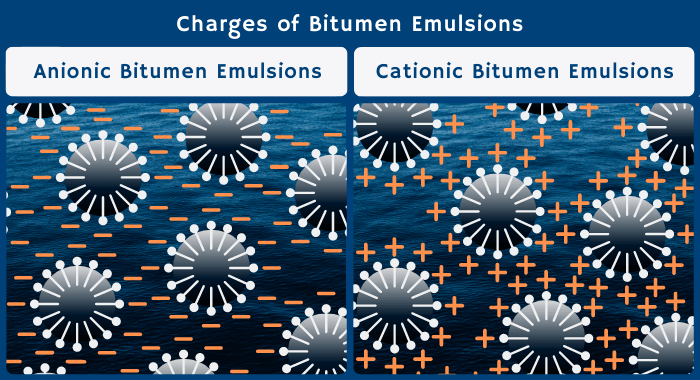
What are the differences between Cationic and Anionic Emulsions?
There are three main differences between cationic and anionic emulsions. The first and most obvious feature is their charge. The second difference is their solubility in distinct systems. The last distinguishing characteristic is their resistance to certain materials.
The manufacturing process of different types of emulsions is distinctive. Thus, not all emulsions are the made the same way. Cationic bitumen emulsions are positively charged while anionic bitumen emulsions are negatively charged. Not only does the surfactant determine the charge of the emulsion, but its choice also impacts the reliability and efficiency of the final product.
Moreover, the types of materials that these emulsions dissolve in are also different. Due to their chemical makeup, anionic bitumen emulsions readily dissipate in high pH or alkaline detergents. On the other hand, they have a good resistance to acids. The opposite is true for cationic emulsions, which have a high tolerance for alkaline detergents and are susceptible to dissolving in acid solutions.
The Setting Times of Bitumen Emulsions
Setting time is a term used to describe the coalescing rate in which the emulsion will bond to its application – the aggregates in a pavement to form a highway, for instance. Most asphalt emulsions fall under one of the following terms for setting time:
- Rapid set (RS),
- Medium set (MS),
- Slow set (SS),
- Quick set (QS).
1) Rapid Set (RS)
Due to rapid setting emulsion’s characteristic of breaking fast, this category has little to no stability. Thus, RS bitumen emulsions are rarely used to mix aggregates. Instead, spray applications like sand and chip seals are the main utility for this type of asphalt emulsion.
2) Medium Set (MS)
The MS emulsions are the mixing grade emulsions. By design, medium set bitumen emulsions are formulated not to break immediately upon contact with graded aggregates. Also, depending on the formulation, this type of asphalt emulsion will continue to retain its workability for a few minutes to several months. Consequently, MS emulsions are valuable in:
- cold recycling,
- patch mixes,
- both cold and warm aggregate mixes, and
- other mixture applications.
3) Slow Set (SS)
They are called slow set because this type of emulsion is stable and takes the longest to break. Due to this characteristic, SS emulsions mix well with fine aggregates while still allowing for extended workability and maximum mixing time. The ultimate objective of this category of emulsions is dense aggregate mixing. Thus, SS emulsions have applications in:
- slurry seals,
- base stabilization,
- soil stabilization
- tack coats,
- dust control and dust palliatives,
- fog seals.
4) Quick Set (QS)
Like the name suggests, quick set emulsions set quickly, like RS emulsions. However, this category of asphalt emulsions is a special one, since very few emulsions fit its 3 criteria. Emulsions can only be classified as QS if:
- they have a reactivity between MS and SS,
- do not need to pass the cement mix test, and
- used in quick-set slurry surfacing applications.
In addition to slurry seals, QS emulsions are designed for situations when a quick breaking time is needed to fix pavements while still minimizing closed traffic time, like micro-surfacing.
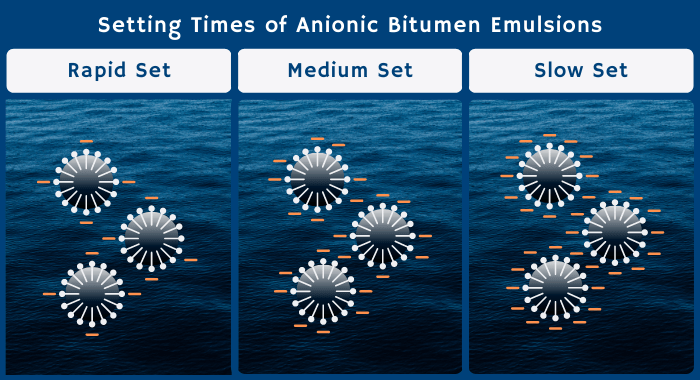
More Information and Resources about Asphalt Emulsions
Still foaming at the mouth for more information about bitumen emulsions? Here are some institutions to check out:
- International Bitumen Emulsion Federation (IBEF),
- The Asphalt Institute and the Asphalt Emulsion Manufacturers Association (AEMA),
- International Slurry Surfacing Association (ISSA),
- Asphalt Recycling and Reclaiming Association (ARRA),
- Foundation for Pavement Preservation (FP2).
Enjoyed this Introductory Article?
Then you will enjoy the related blog posts below:
- 5 Reasons to Use Anionic Bitumen Emulsions over Cationic Emulsions
- Carbofen is a Vinsol Resin Substitute
- The Power of the Pine Knot
Published on 13-MAY-20. Last updated on 10-JUN-21.
1 thoughts on “An Introduction to Bitumen Emulsions”
very good!!!
Comments are closed.